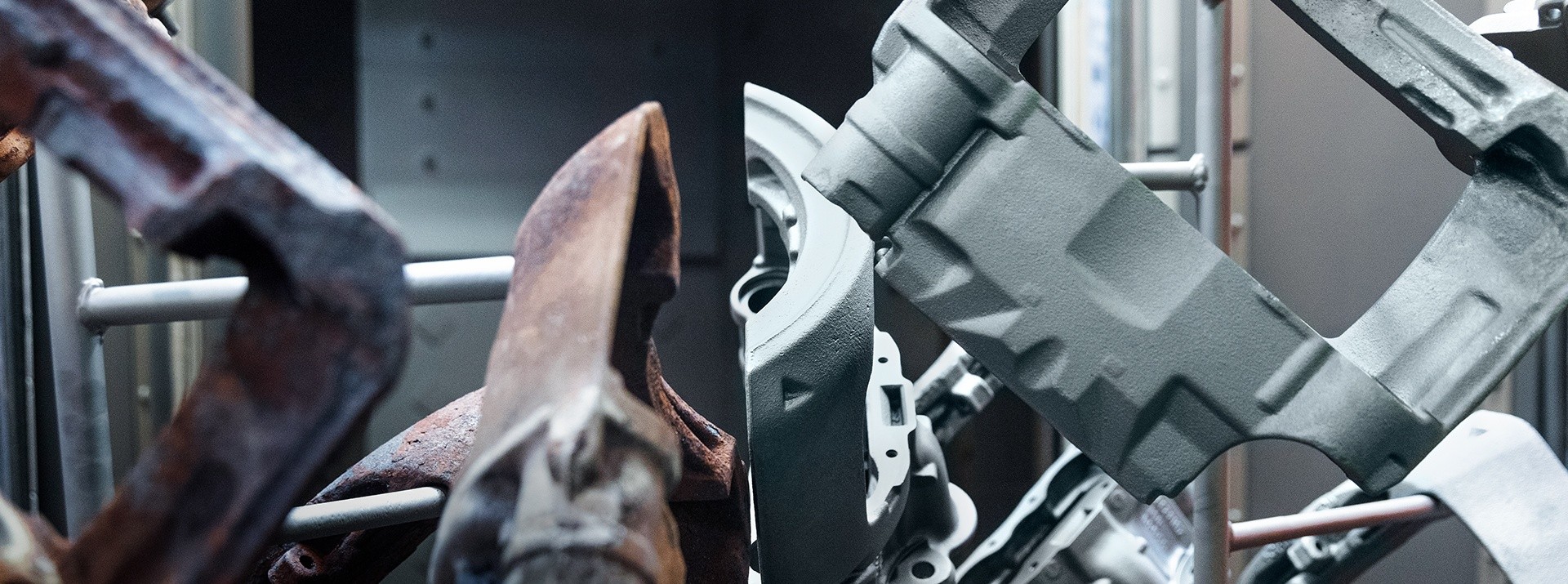
At Knorr-Bremse TruckServices, we are committed to providing the best core management for commercial vehicles, while also prioritizing sustainability and cost-effectiveness.
The main driving forces behind this philosophy are:
- Ensuring the availability of high-quality Knorr-Bremse EconX® (genuine remanufactured) products in the marketplace.
- Preventing broken, damaged, or worn-out safety-critical products from being misused for reconditioning activities by unauthorized parties.
- Protecting customers from potential safety issues that could arise from incorrect/unauthorized parties repairing or reconditioning activities.
- Promoting a circular and sustainable economy by minimizing waste and CO2 emissions. Each returned Core is contributing to savings of up to 150kg CO2 equivalents and recovery of 80% raw material.
Core buy-back program
Contact us for more information!
Do you have old truck parts in your possession like a compressor, air disc brake, clutch actuator, aid dryer, EBS, etc? Contact us for more information on our core management and remanufactured truck parts offerings, or to inquire about core return instructions and return logistics.
We look forward to partnering with you in your truck parts journey.
Remanufacturing - the highest form of recycling
Remanufacturing is the industrial reconditioning of cores (used products) and thus the highest form of recycling and circular economy. The key to success for a business model of this kind is a customer-friendly process for returning the cores, which are the limiting resource, to the remanufacturing plant. This is normally facilitated through a core deposit program.
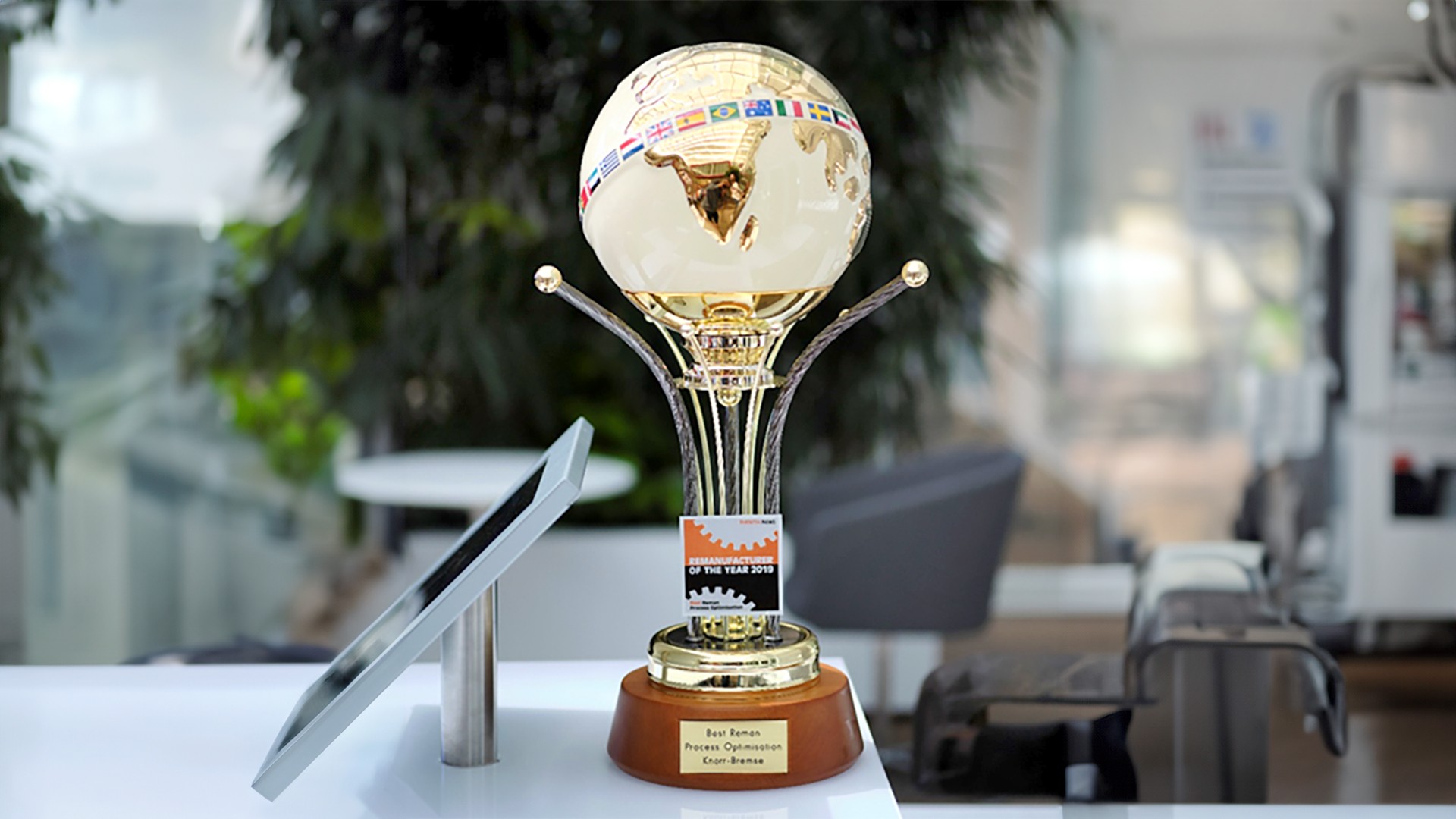
Remanufacturer of the Year Award for Best Reman Process Optimisation
In 2019, during the world’s largest remanufacturing exhibition, ReMaTec in Amsterdam, Knorr-Bremse TruckServices received the Remanufacturer of the Year Award 2019 in the category “Best Reman Process Optimisation”. The panel of judges commended the performance of Knorr-Bremse TruckServices in the field of process optimization. Through its fully digitized return process for cores, the jury said, Knorr-Bremse TruckServices was living up to the high expectations of customers and of the process itself. The jury were particularly impressed by the way in which the Knorr-Bremse process permits the seamless tracking of a core, from collection order and incoming goods, to core identification and deposit refund accounting.
Core Program and Procedures
At Knorr-Bremse TruckServices, we prioritize the importance of cores in the remanufacturing process. Cores are essential to our efforts in producing high-quality Knorr-Bremse EconX (genuine remanufactured) products while promoting circular economy.
Knorr-Bremse Core Return Policy and Strategy
Our core policy and strategy are guided by three main objectives:
- Quality Assurance: We collect high-quality cores to ensure the availability of top-notch Knorr-Bremse EconX products in the market.
- Safety: We prevent unauthorized parties from misusing broken, damaged, or worn-out safety-critical products for reconditioning. This approach safeguards customers from potential safety issues that may arise from incorrect or unauthorized repair activities.
- Environmental Responsibility: We promote a sustainable economy by reducing waste and CO2 emissions. Every returned core contributes to savings of up to 150 kg of CO2 equivalents and the recovery of 80% of raw materials.
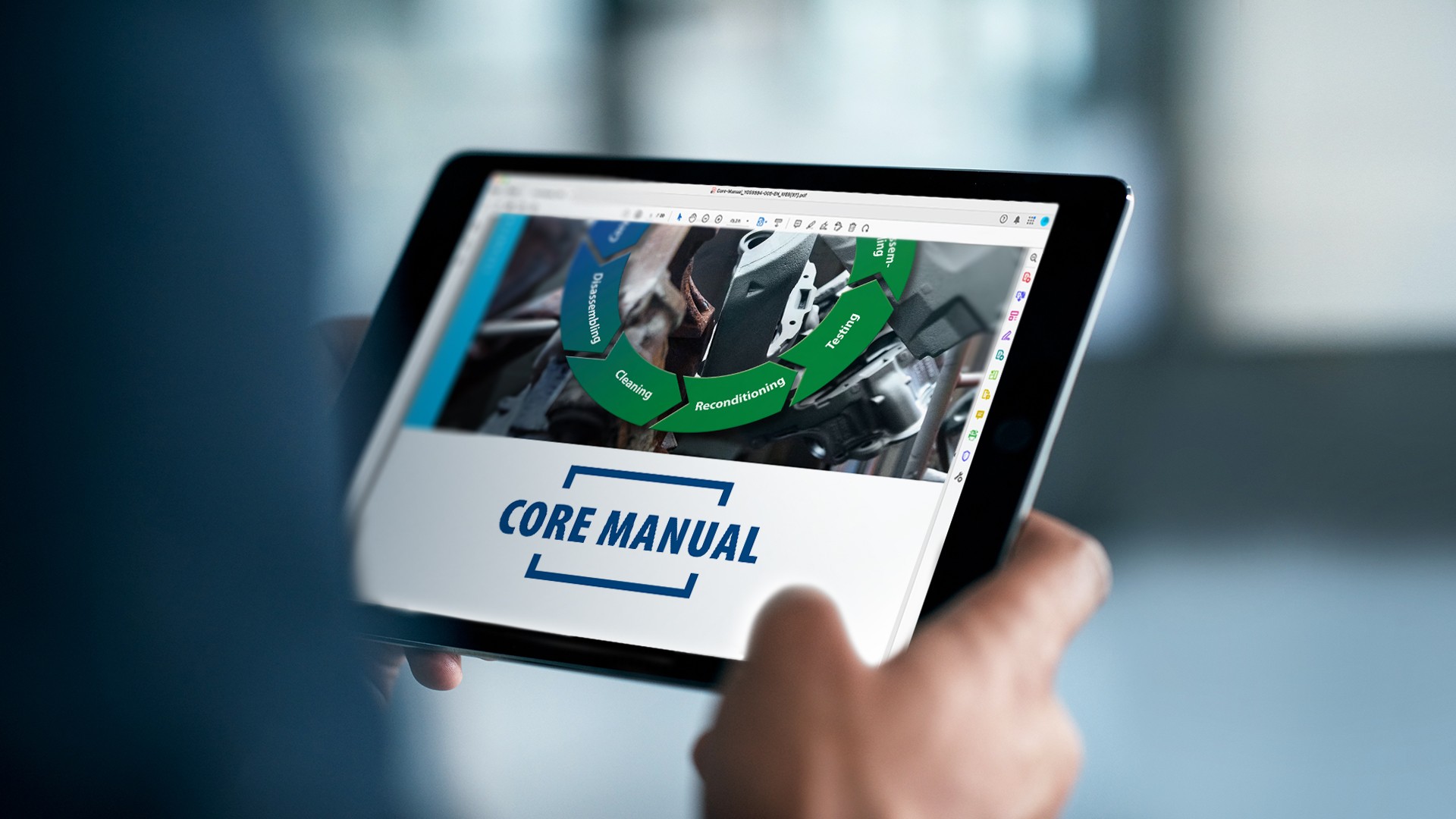
If you want to find out more about our Core Program, here you can find the Guideline.
Download Core ManualThanks to Remanufacturing, in 2024 we saved:
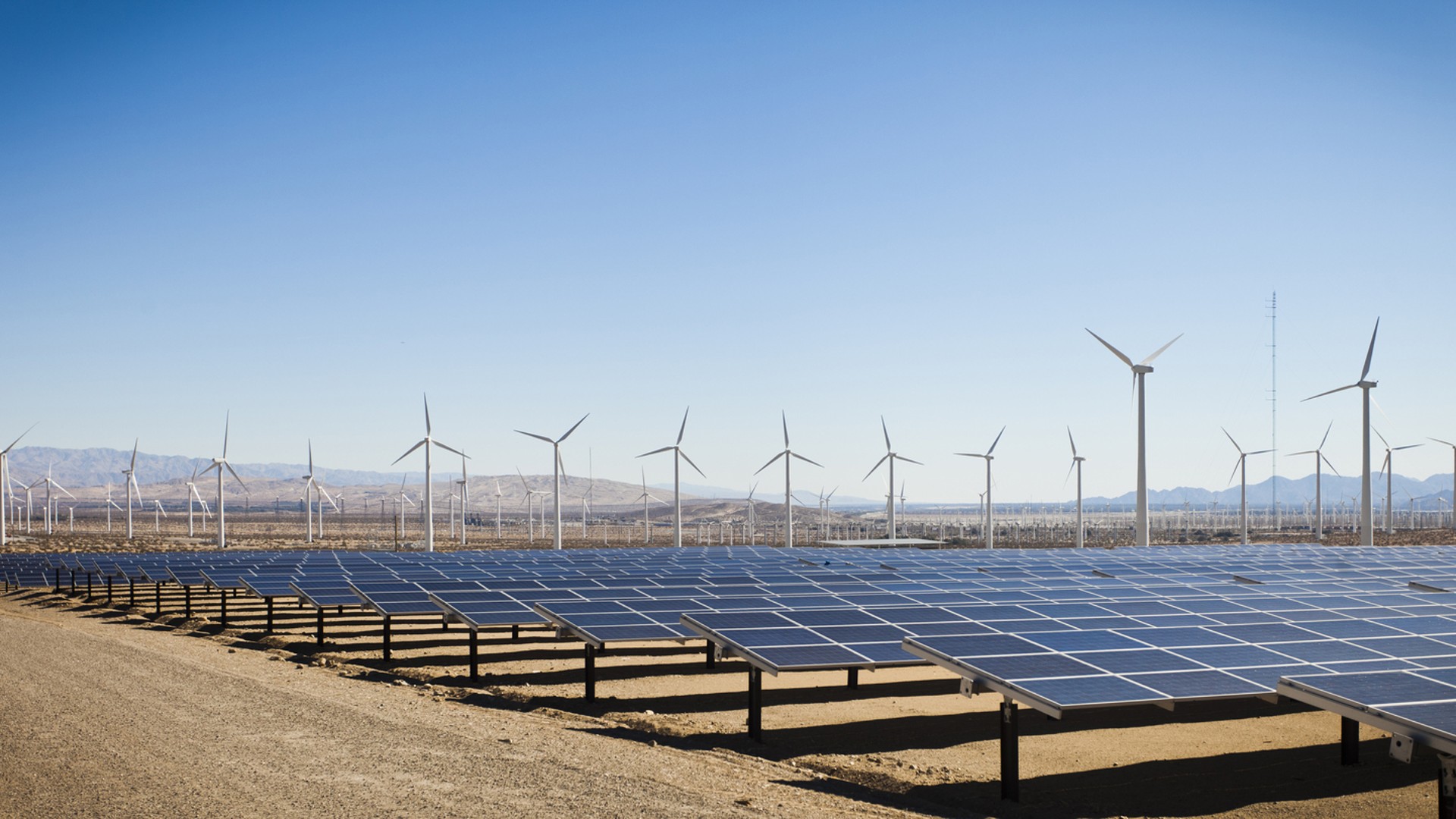
Equales to *111.516 m² solar panels = appr. the size 16 football fields
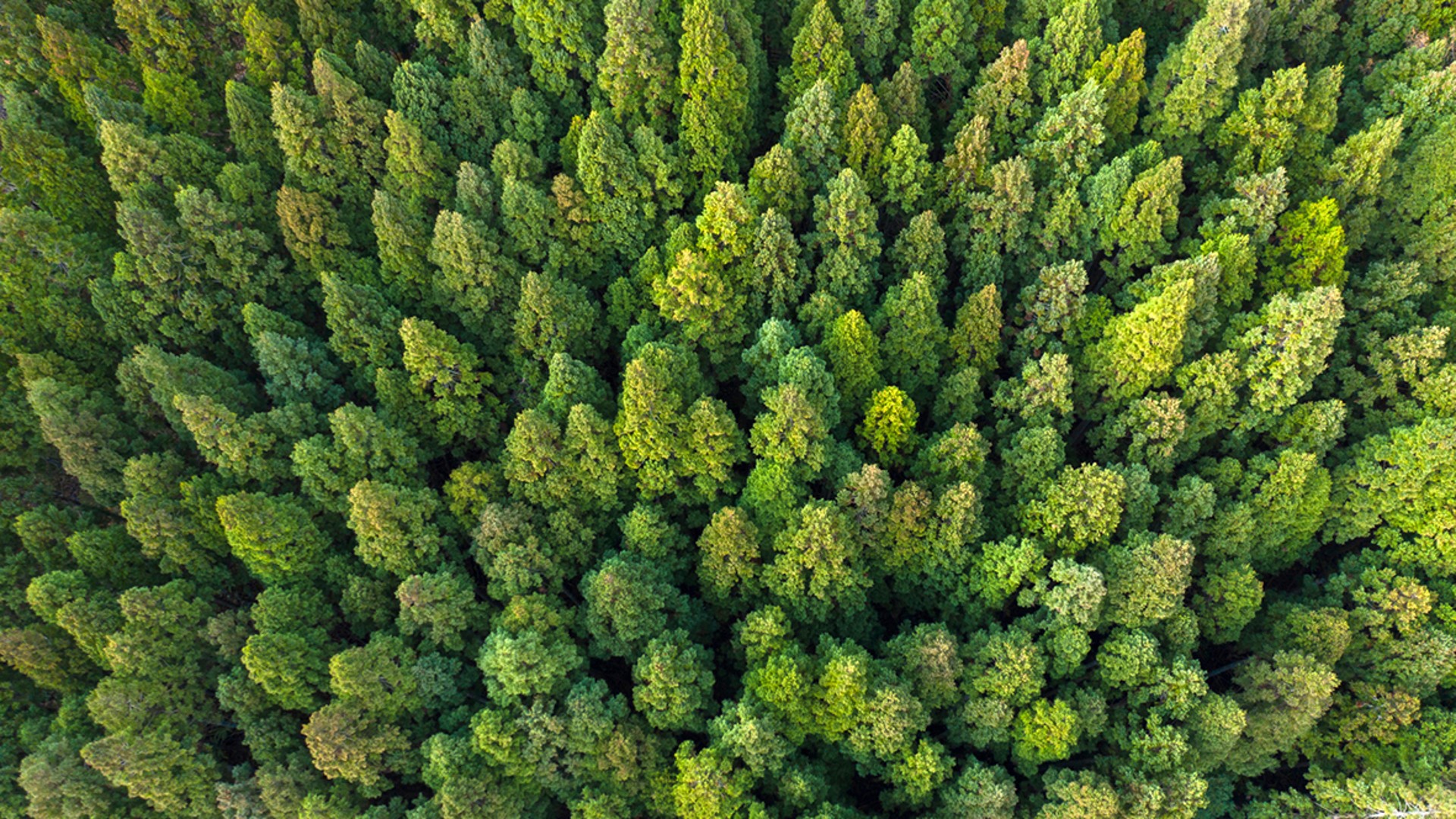
*351Ha of forest = appr. the size of Central Park, New York
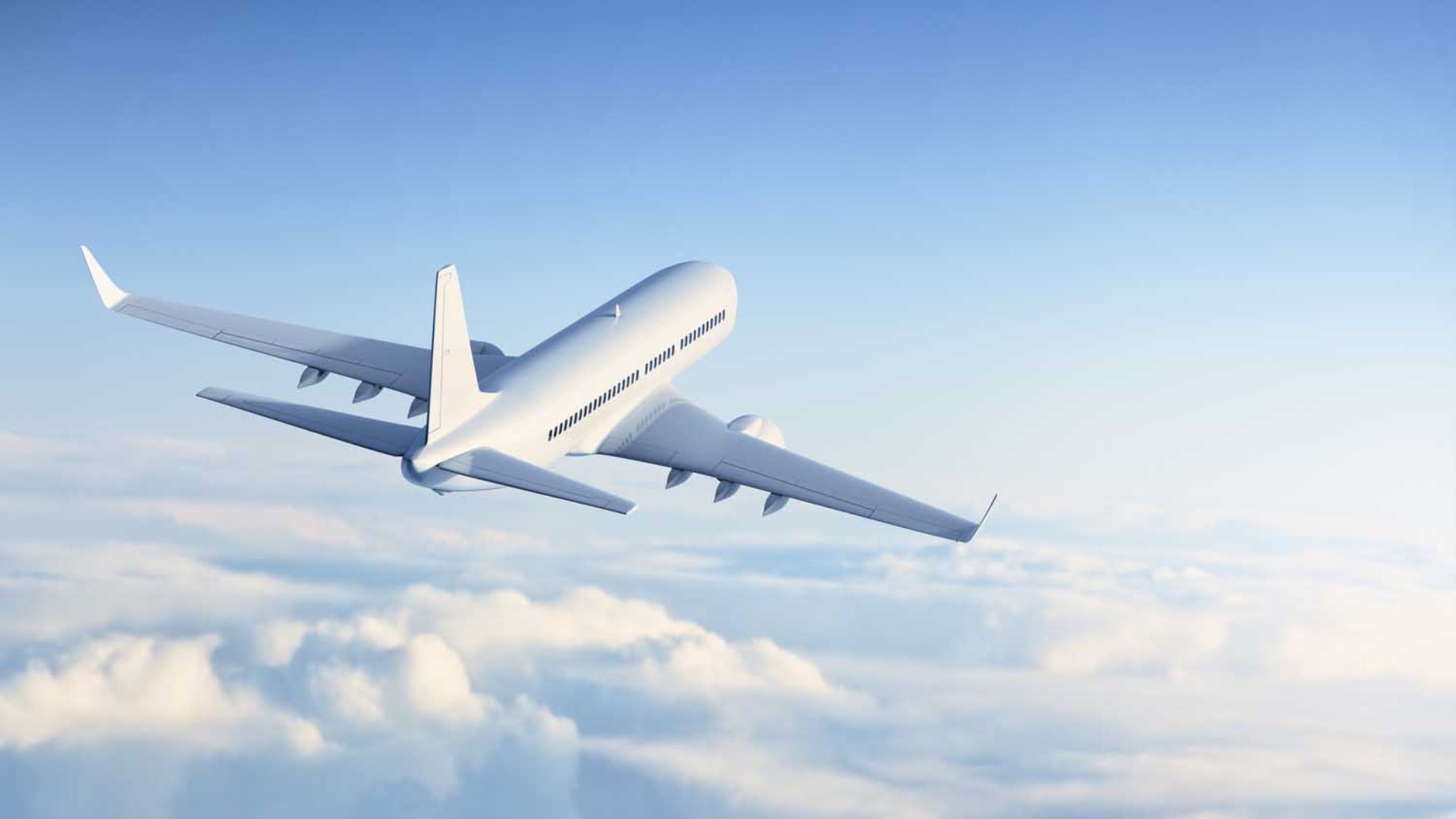
*Weight of 17 fully loaded A320s
How can the end users contribute to keeping the quality of returned cores?
End users play a crucial role in preserving core quality by following specific guidelines:
- Adhering to the Core Damage Prevention Guideline and Core Manual provided by Knorr-Bremse.
- Storing cores in dry, clean spaces post-vehicle disassembly to prevent corrosion.
- Ensuring proper packaging and protection of threads/ports during transit, complying with local regulations.
- Preferably returning cores in the packaging of the replacement product.
- Arranging cores for transport with heavier ones at the bottom and lighter ones on top, separated by interlayers for safety.
- The sender is obliged to ensure that the packaging and its contents are following local laws (e.g. of EU).
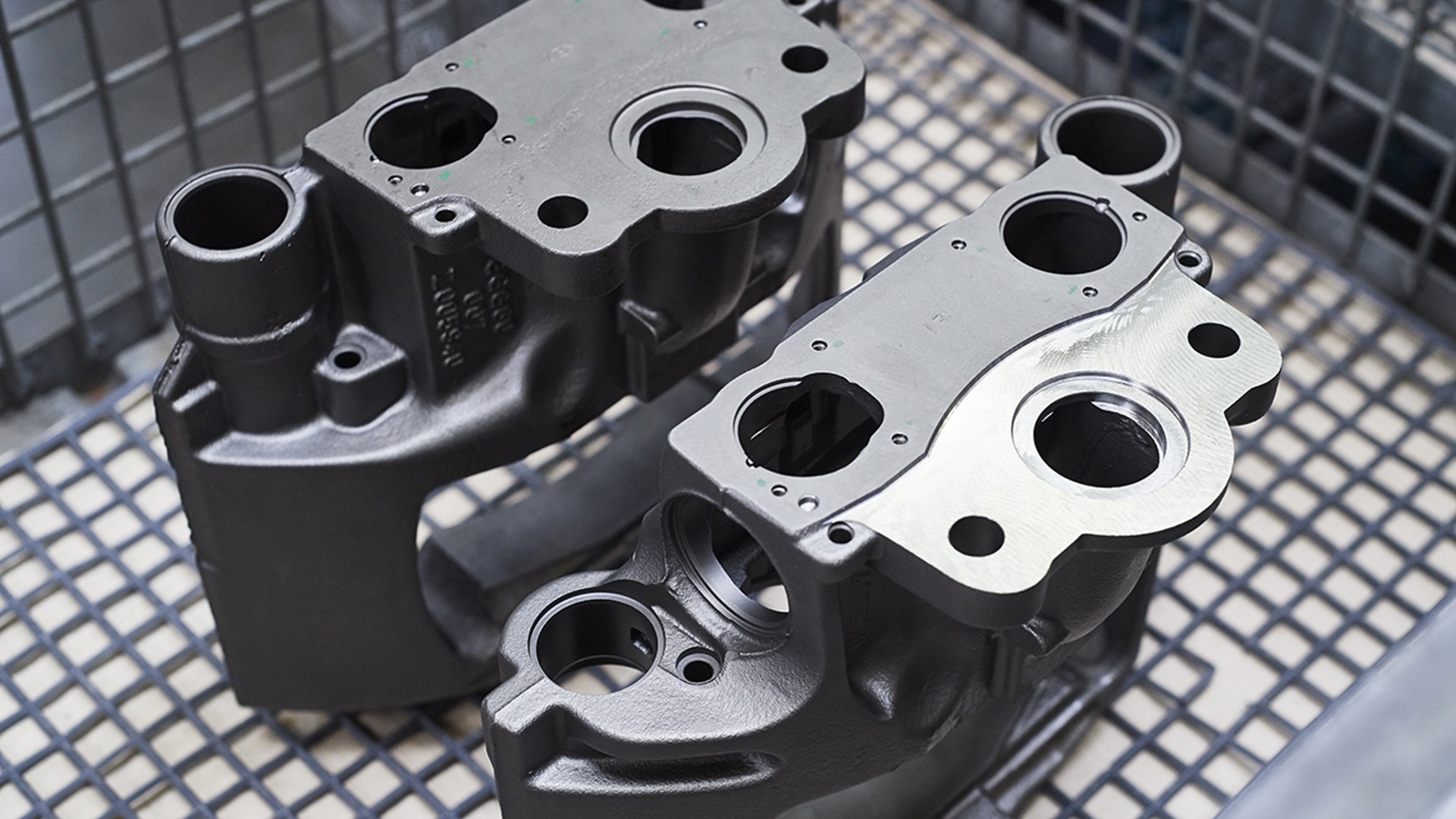

Advantages for Customers
- Customers can save money on repairs and maintenance by using remanufactured parts, which are often less expensive.
- Core management ensures that returned cores fulfil certain quality criteria, guaranteeing that consumers receive high-quality remanufactured components that work similarly to new parts.
- By efficiently managing cores, manufacturers can ensure an ongoing supply of reprocessed components, reducing downtime for customers who are waiting for core replacements.
- Remanufactured parts support sustainability by reducing the waste and preserving resources.
Core Return Processing at a glance
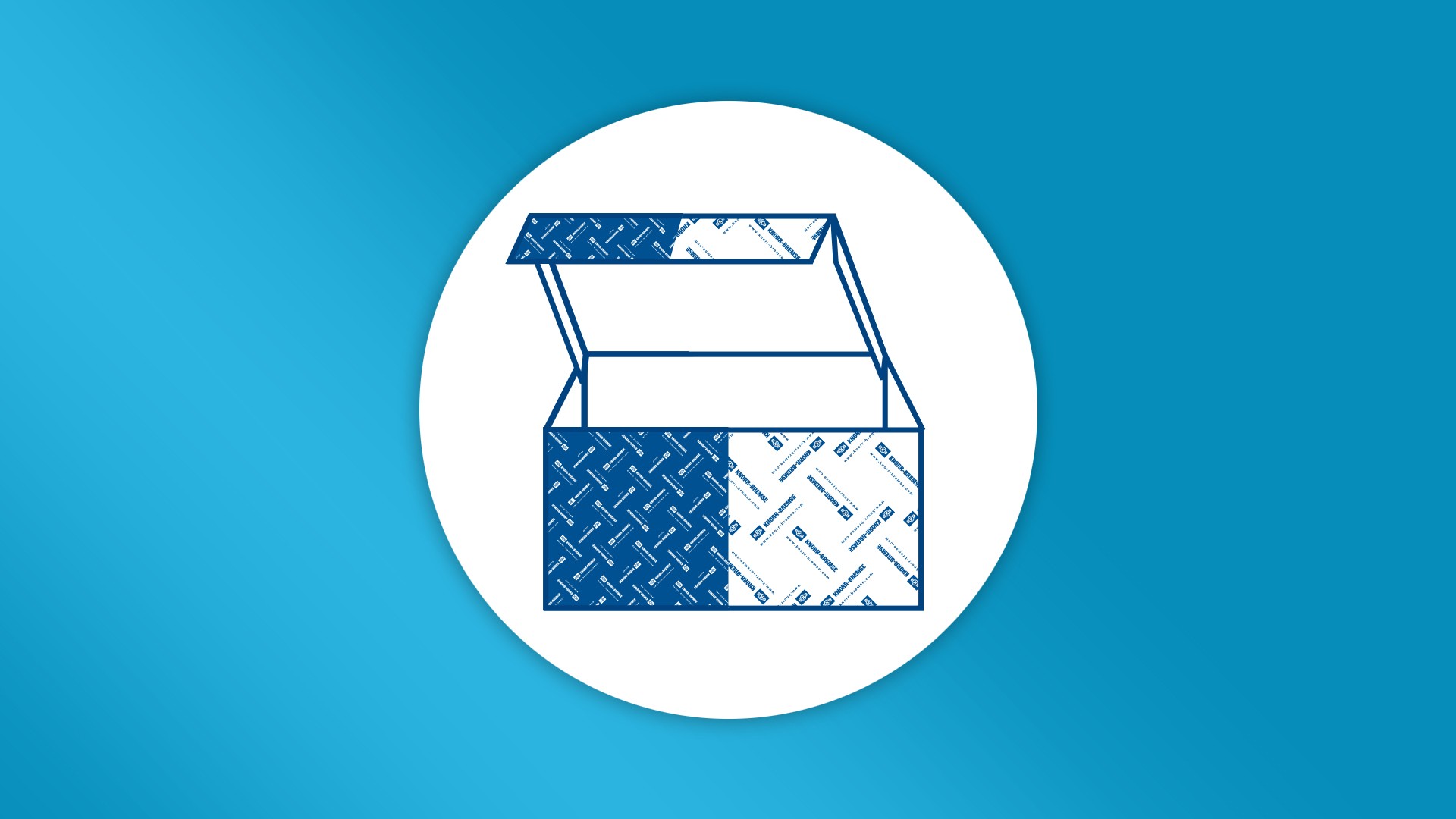
Step 1: Collect & Pack
Collect Cores and pack them according to the Packaging Guideline.
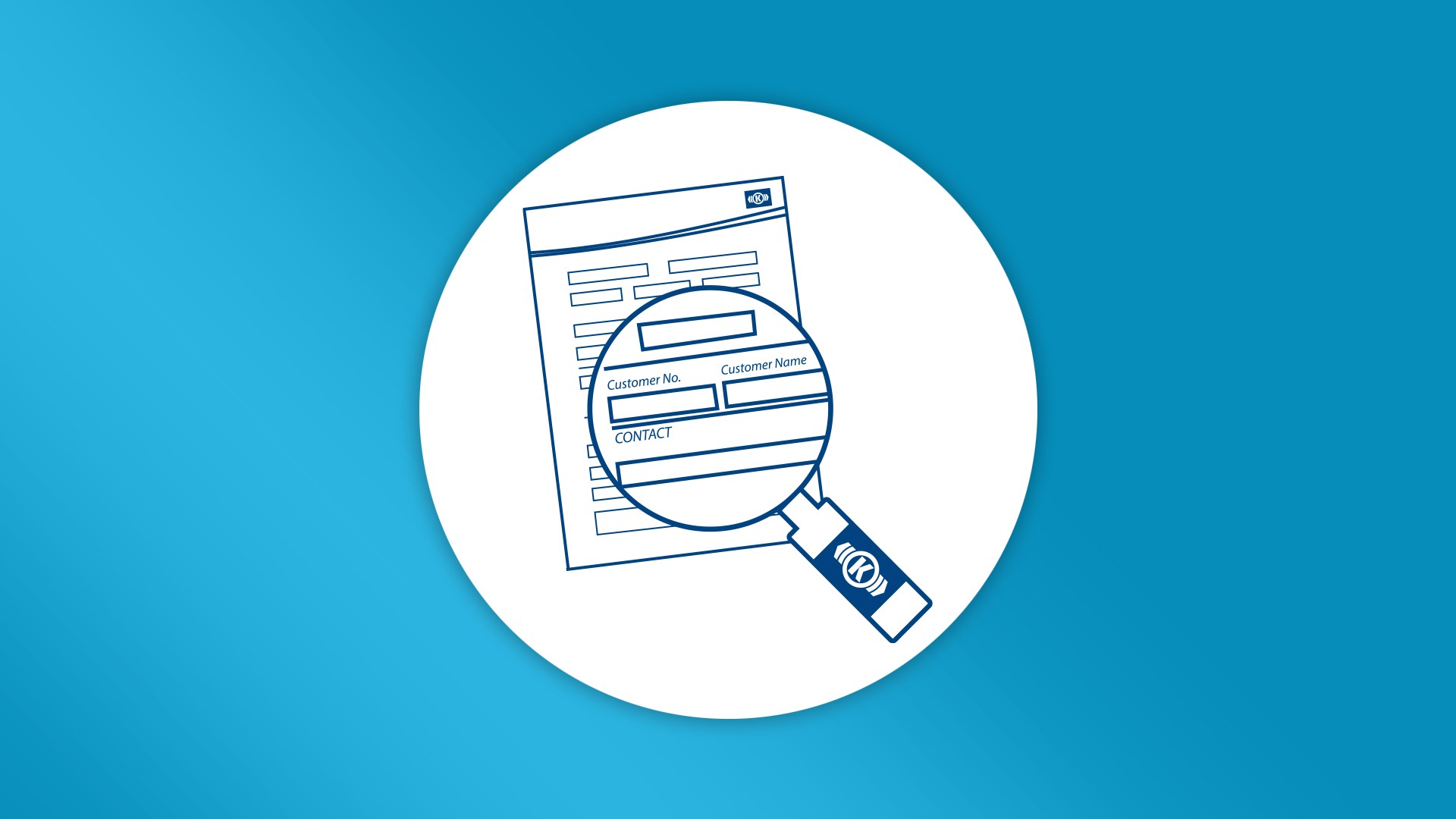
Step 2: Collection Request
Option a: Online via TruckServices Customer Portal Option b: Via Email
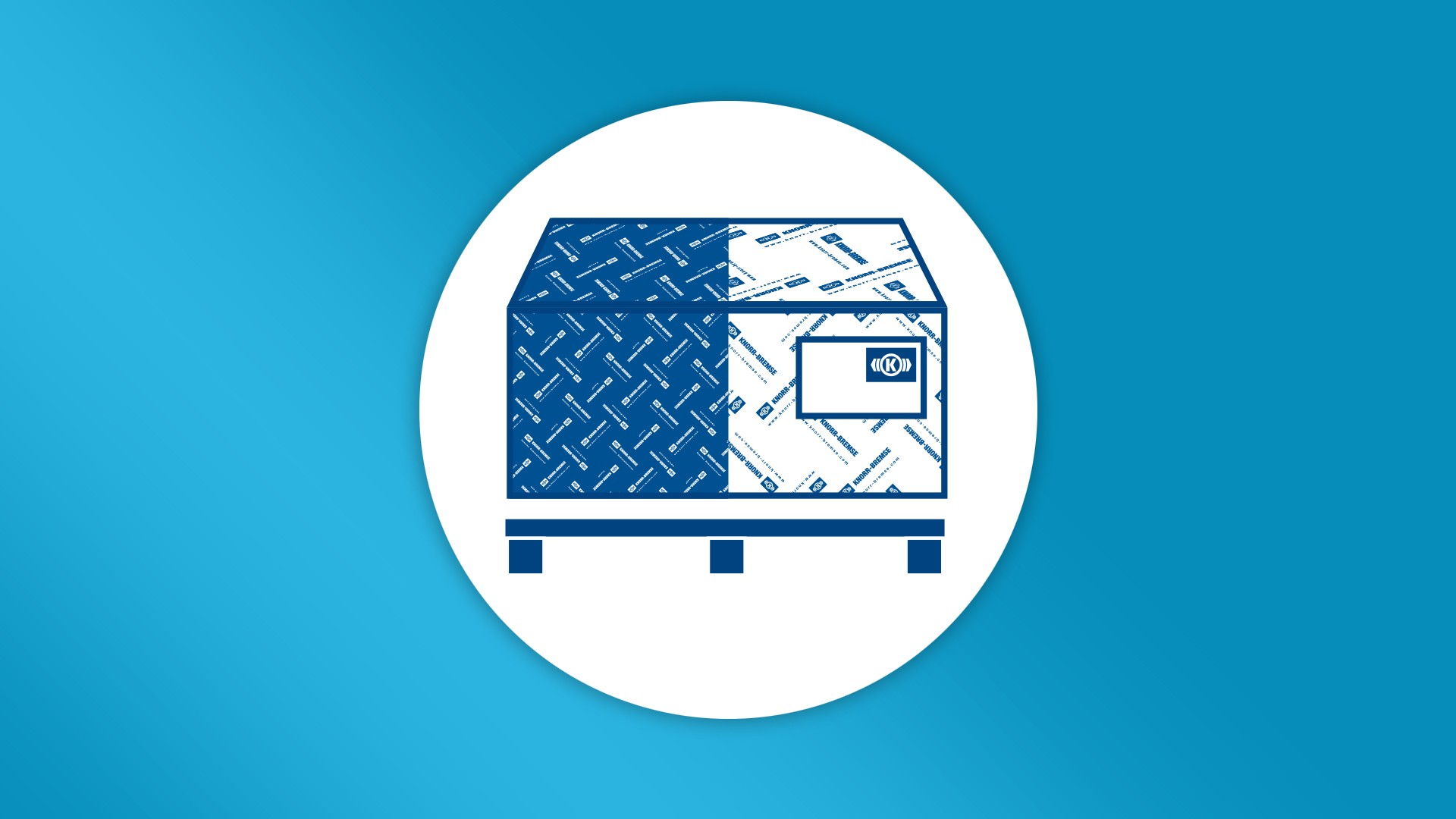
Step 3: Identify each pallet
Print out the Core Return Request form including the CRM number. Attach the form in an envelope outside and inside each box.
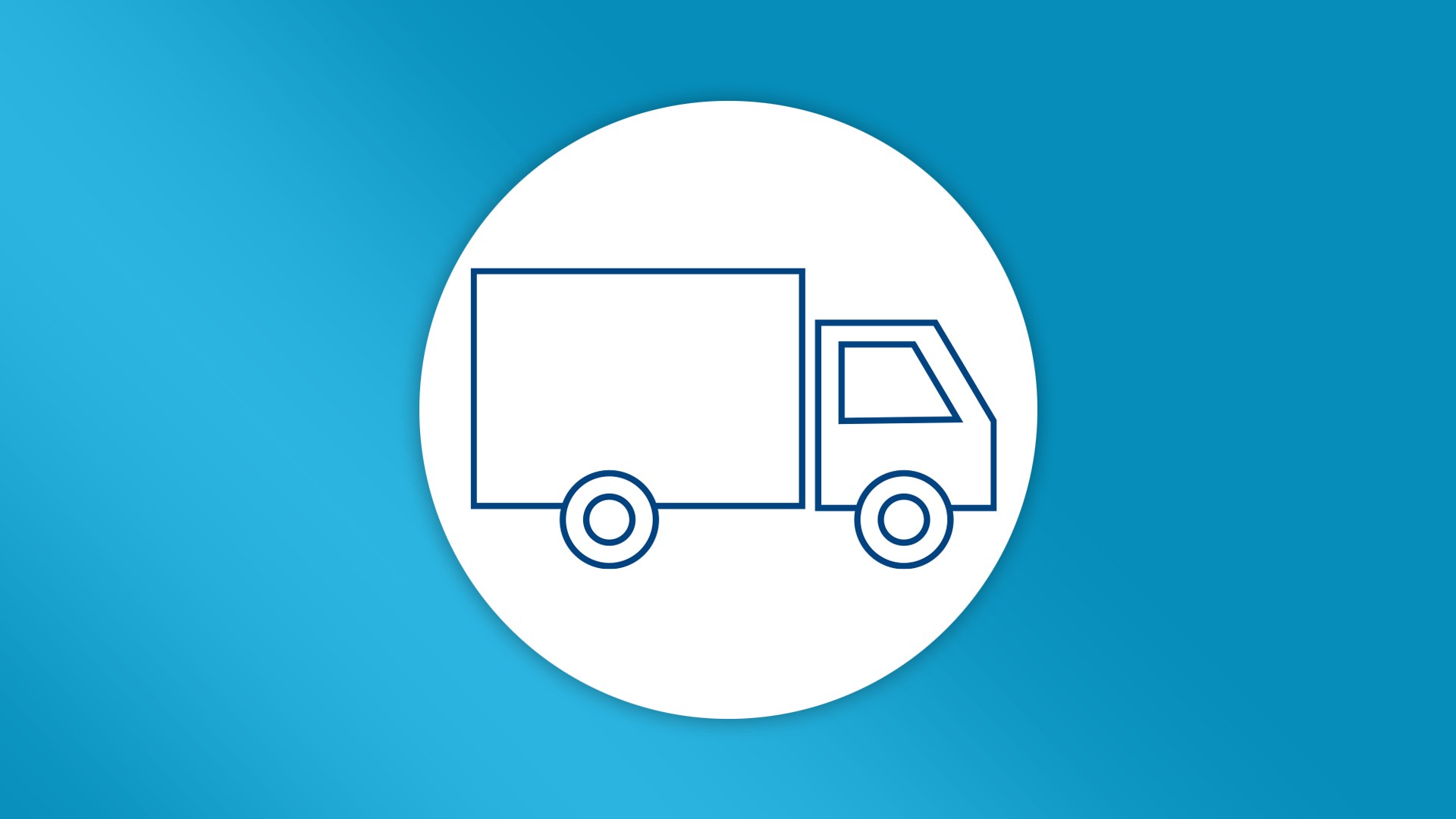
Step 4: Send the shipment
Prepare the Core shipment for collection.
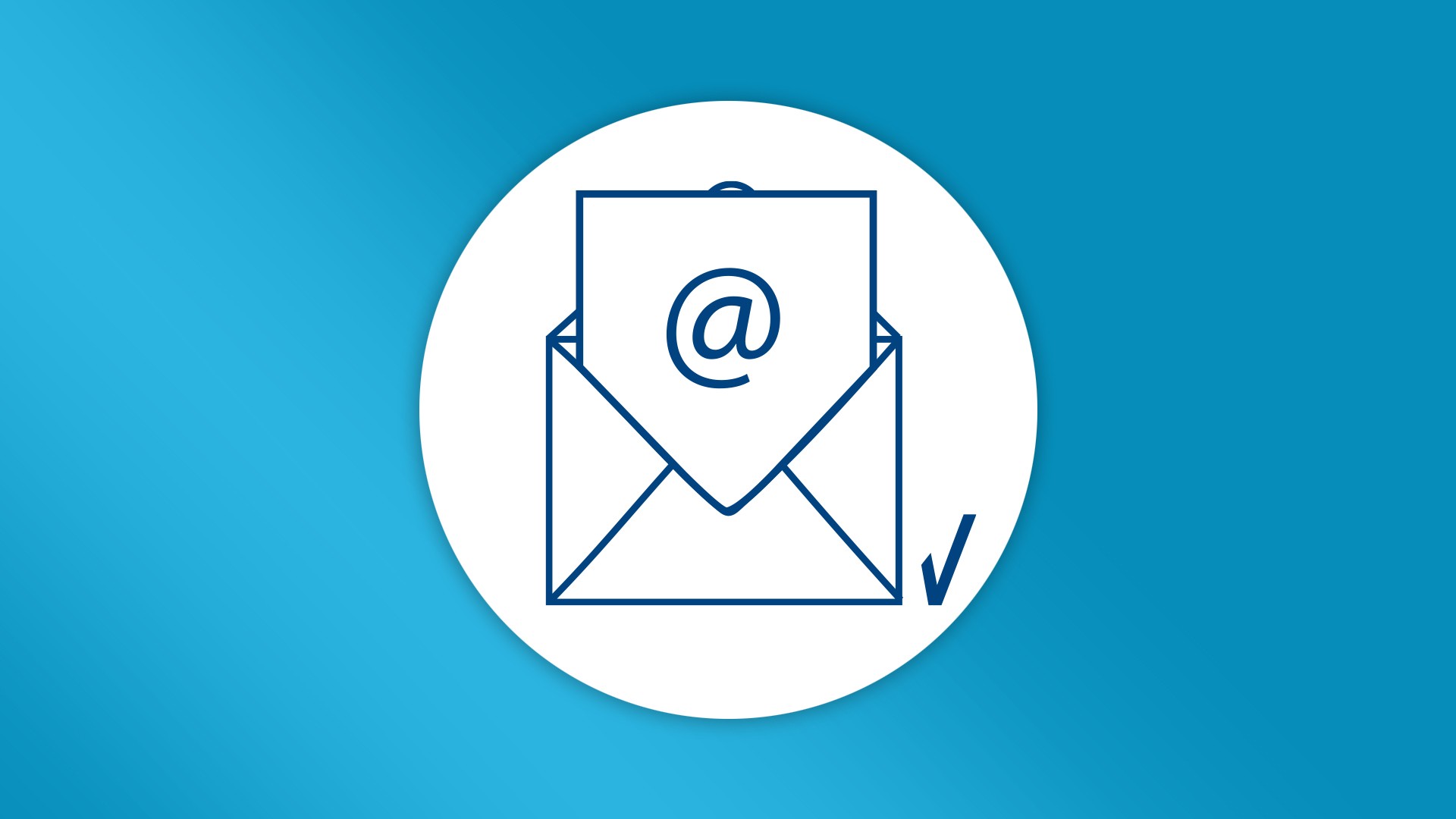
Step 5: Check the Acknowledgement note
After the shipment has been sorted and Cores have been graded, a Core Acknowledgement Report is emailed. The Report shows the accepted or rejected quantity per Core Group in comparison with the initial collection request (the CRM no. can be used as a reference).
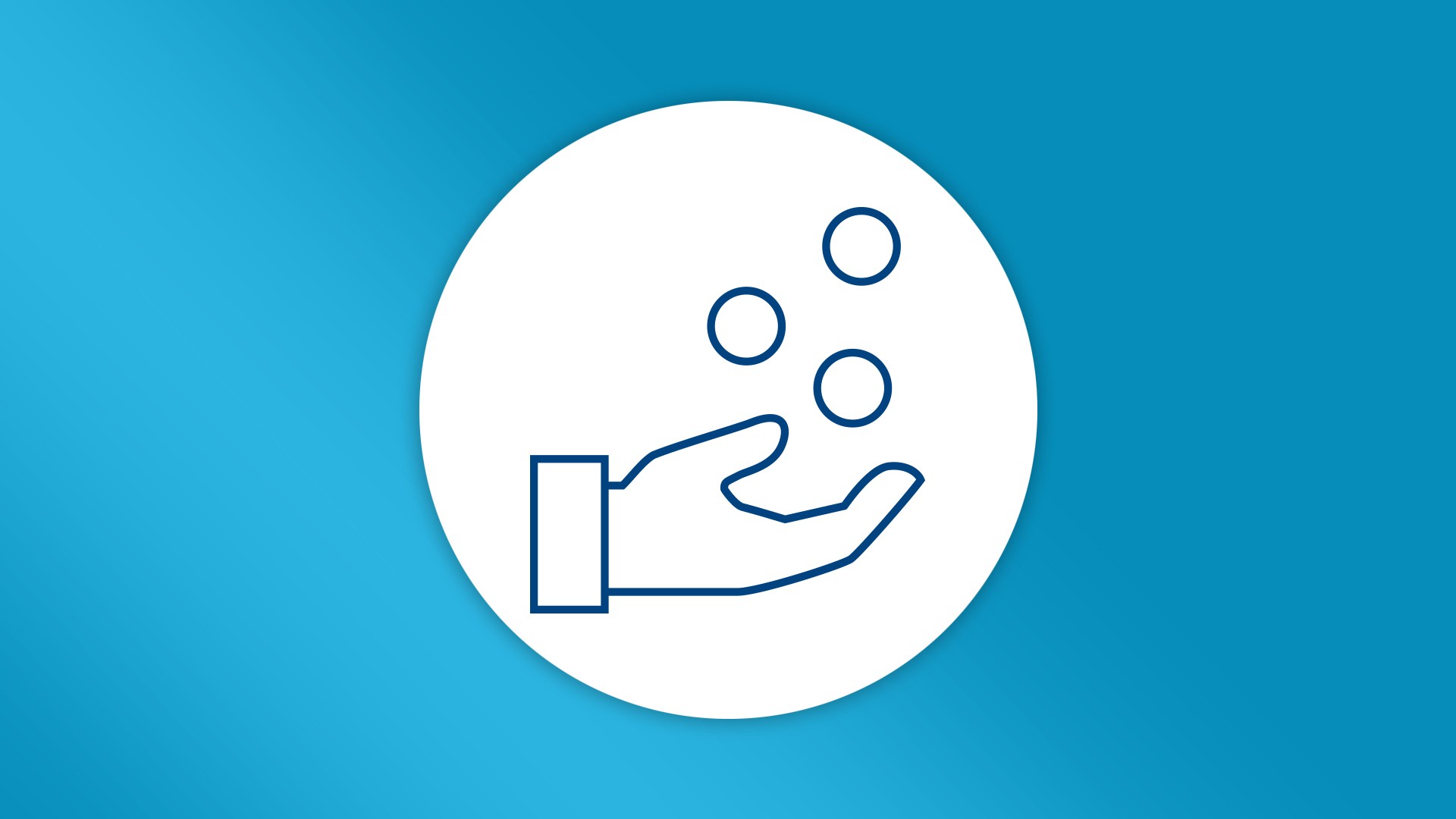
Step 6: Get the Core Deposit self-billing invoice
The Core Deposit is credited if the returned Core meets the Core Acceptance criteria and relevant Core Deposit purchase exists on Core account. The monthly Core Summary Report shows the Core Account status, accessible via TruckServices Customer Portal or sent by email.